Reg Smith's Music Box Restoration Work
We asked Reg Smith to say a few words about his music box
restoration work and the ways in which MD is helpful to him. He gave
us a recording of a music box (streaming) that you can listen
to with an MP2/3 player.
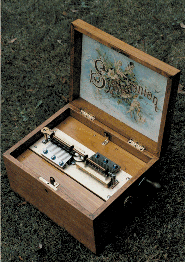 |
SYMPHONION 8" disc playing music box made ca.
1896 near Leipzig, Germany.
What I do is full restorations of 19th century cylinder and disc
music boxes. In case you aren't familiar with them, I will try to
explain... The cylinder boxes were made between 1810 and about 1900,
and consisted of a brass cylinder studded with thousands of very tiny
steel pins, which plucked a tuned steel music "comb" as the cylinder
was rotated by a clockwork (spring) motor. Cylinders ranged in length
from about two inches to nearly two feet, and up to five inches
diameter. They were always extremely labor intensive to produce,
being mostly hand-made almost exclusively in Switzerland.
The sound they produce, especially the machines made during the
earlier years (1830 - 1865), is absolutely without equal in our modern
world; there is nothing electronic that can even come close to the
ethereal sounds of a properly restored instrument. Many of the
earlier ones play operatic arias or overtures in such fantastic detail
and with arrangements which are so incredible one would be sure those
long ago craftsmen must have been musical geniuses. I have seen
several people actually get tears in their eyes at a first
introduction to a fine example of this "lost art".
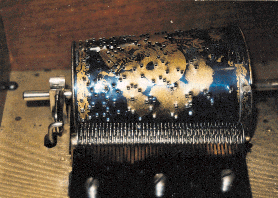 |
1895 CAPITAL "Cuff" box, made in Jersey City, New Jersey, so named for
the metal music cones which at that time resembled fashionable men's
shirt cuffs. The Capital was an atypical design; a hybrid of the
earlier cylinder and the newest disc playing machines. Capitals were
only produced for about two years and are today extremely scarce and
highly prized by collectors.
In 1886, a new type of music box appeared in Germany - the disc
playing music box. The emergence of this format in a number of ways
parallels the modern introduction and subsequent takeover of the LP
record by the compact disc. Cylinder music boxes, while musically
fabulous, had the major drawback of being only able to perform the
tunes which had been "pinned" to the cylinder originally. Thus, once
a family had heard the 4, 6, 8, or 12 tunes their machine's cylinder
could perform, dozens of times, it obviously would get tiresome, and
the machines would often be relegated to closets or at least not
played mushc anymore. The brand new disc playing machine solved this
problem by allowing the owner to quickly change tune discs almost
instantly.
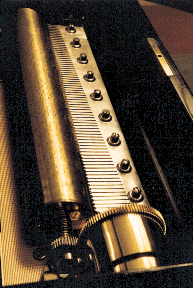 |
Freshly repinned and restored BREMOND 13" cylinder music box, was made
in Geneva, Switzerland in 1879. This fine example plays 8 tunes in the
style of a mandoline.
With thousands of new titles being released each month, and since
these new metal "records" could be cheaply mass produced, almost
overnight the music box became something almost any family could
afford to enjoy, whereas the earlier cylinder type had always been
affordable only by the very affluent because of its extreme high cost
of manufacture. As with the CD / LP phenomenon, disc music boxes
caught on like wildfire and by 1890, it was getting hard for cylinder
box manufacturers and vendors to "dump" inventory. In 1894, the
Regina Company was founded in Rahway, New Jesey to make disc boxes and
these were an overnight runaway success. Even today, Regina music
boxes are considered among the finest ever made by most collectors.
Back to your original question... When a customer sends an old
music box to me for repair, it is typically covered with rust,
corrosion, and all manner of dirt; an accumulation of more than a
century. Cylinder pins are often broken off which requires a total
"repinning" of the entire cylinder- the remnants of old pins are
etched away in an acid solution, which leaves a bare brass cylinder
with thousands of nearly microscopic holes into each of which I must
drive a brand new steel pin. Yes! One at a time!!
A typical cylinder of say, 13 inches length usually will have more
than 10,000 pins. Also, the tuned music combs often get broken teeth
which must be replaced and properly tuned. This work is so tedious as
to defy description; it usually takes 8 - 12 hours work to make just
one replacement tooth, solder it in to the comb and tune it in such a
way that it sounds perfect and the repair joint is nearly invisible to
the naked eye. Yes - this work is not cheap. But it is magical and
rewarding to see and hear each one when it is all restored since each
cylinder box is absolutely unique (there were no duplicates as far as
is known today).
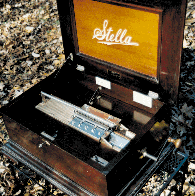 |
A completely restored 1899 STELLA 15" disc machine, with twin combs,
made by Mermod Freres in St. Croix, Switzerland. This particular
machine still bears the brass dealer's tag from the shop where it was
originally sold in South Carolina at the turn of the century.
Thus, it is very important that I can make a reference audio
recording of each machine at the time it arrives as an invaluable aid
to tuning later on after all the filth and rust or corrosion has been
safely removed. MiniDisc's random access allows me to instantly find
a certain tone, for say a certain tooth of a certain comb, and also
allows me to easily repeat that tone at will. Likewise, I can make
extremely accurate recordings (no wow and flutter, or audible
distortion or coloration of the tones of the original instrument).
Tape recordings just can't do the same job at all.
Also, I like to make "after" recordings (when I am all finished
with a given job) and locate them immediately after the "before"
recordings for comparitive purposes. Sometimes I make recordings of
other collectors' music boxes and it is great to be able to edit
(delete) tracks of boxes that for whatever reason don't sound so
great. None of these features would be possible with tape. I have
been recording music boxes as they passed through my shop for almost
six years now and I LOVE MiniDisc. I use two Sony mics: the ECM-957
and ECM-717 for my recordings, whether in the shop or in private
homes. I get fabulous results. I used to use the MZ-1 but now use
an MZ-RH1. All the pictured machine's
restorations required major comb repairs and retuning for which I used
MD recorders extensively. MiniDisc technology has proven to be an
invaluable tool for effective and accurate voicing of these old music
combs.
- -Reg Smith (musicboxrestoration@gmail.com)